Tungsten Radiation Shielding Machining
.jpg)
Tungsten radiation shielding machining process mainly includes forging, heat treatment, mill finish, polishing, turning, making thread, holed and so on.
Forging:
Tungsten and several tungsten alloys have been successfully forged over a wide range of temperatures from as low as 1800 to 3500F. In rocket nozzle forging, a billet height reduction of approximately 80% at forging temperatures below the critical recrystallization temperature is considered essential. This imparts the fine-grained, fully wrought, fibrous structure that is characteristic of high strength and good ductility at low transition temperatures.
Tungsten is generally forged in the hot-cold work temperature range where hardness and strength increase with increasing reductions. Both systems exhibit increasing forgeability with decreasing grain size.The greatest use for tungsten forgings has been in rocket nozzle applications. Production forging of tungsten nozzle inserts has been largely limited to billets prepared by powder metallurgy techniques because of their earlier availability than cast tungsten.
Heat Treatment:
Heat treatment is a group of industrial and metalworking processes used to alter the physical, and sometimes chemical, properties of a material. The most common application is metallurgical. Heat treatment involves the use of heating or chilling, normally to extreme temperatures, to achieve a desired result such as hardening or softening of a material. Heat treatment techniques include annealing, case hardening,precipitation strengthening, tempering ,normalizing and quenching. It is noteworthy that while the term heat treatment applies only to processes where the heating and cooling are done for the specific purpose of altering properties intentionally, heating and cooling often occur incidentally during other manufacturing processes such as forging.
Polishing:
Polishing is the process of creating a smooth and shiny surface by rubbing it or using a chemical action, leaving a surface with a significant specular reflection. The process of polishing with abrasives starts with coarse ones and graduates to fine ones.
Polishing is using polishing tools and abrasive particles or other polish media to process the surface of tungsten shielding. Polishing can not improve the accuracy of size or geometric shapes of material, but aim to obtain a smooth surface or specular gloss. Sometimes, polishing is used to remove the specular gloss. Tungsten materials are polished with emery, which is belong to the crude polishing. Fine polishing required to polish with polishing agent, water and emery. Polishing agents generally contain diatomite, sintered or non-sintered alumina and iron powder.
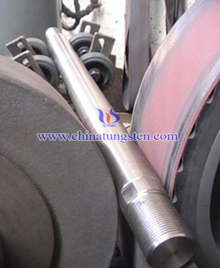
Turning:
Turning is an engineering machining process in which a cutting tool, typically a non-rotary tool bit, describes a helical tool path by moving more or less linearly while the workpiece rotates. The tool's axes of movement may be literally a straight line, or they may be along some set of curves or angles, but they are essentially linear (in the nonmathematical sense). Usually the term "turning" is reserved for the generation of external surfaces by this cutting action, whereas this same essential cutting action when applied to internal surfaces (that is, holes, of one kind or another) is called "boring". Thus the phrase "turning and boring" categorizes the larger family of (essentially similar) processes. The cutting of faces on the workpiece (that is, surfaces perpendicular to its rotating axis), whether with a turning or boring tool, is called "facing", and may be lumped into either category as a subset.
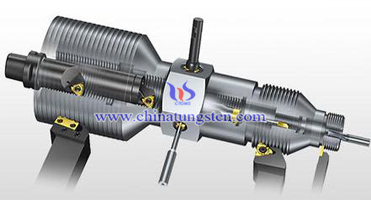
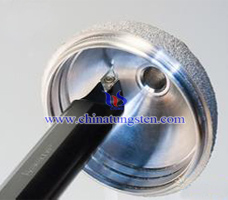